Pyrolysis is a technique that uses heat to convert plastic waste and used tyres into usable products, such as oil and carbon black. Continuous pyrolysis plant is designed to work without interruption with equipment for correct burning and will have several parts that are all interlinked to maintain the continuity of operations.
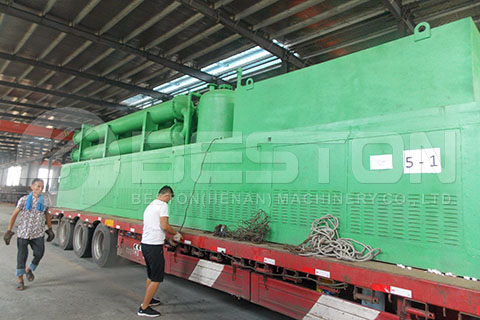
A continuous tyre pyrolysis plant will have to start with an extruding system that makes a hot mass of the tires so that they can be easily be fed into the pyrolysis reactors. Often to facilitate these they may have shredders and other equipment that breaks the tyres down into small bits of 20 mm size or less, and also helps to remove any steel in the tires. Steel is commonly used in radials. This steel can then be recycled separately. The reduced size of the shredded rubber increases the area available in the waste to absorb the heat that it has to go through, and helps to speed up the process of pyrolysis.
The waste rubber than moves to the continuous feeding system that ensures that the pyrolysis reactor has waste matters continually available in them at optimum rates that ensure complete burning of the ease material. These feeders can be conveyors or screw mechanisms that move at a rate that feeds the waste that is within the capacity of the plant.
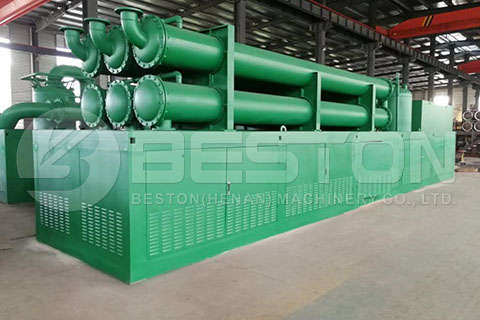
The reactor is the most important part of the continuous pyrolysis plant and consists of a closed vessel in which the waste rubber is burnt with the use of fuel like wood, oil, gas, or others. This burning is carried out in the absence of oxygen and creates oil gas when the temperature reaches 120 degrees Centigrade.
The gas then moves to the gas package which stores the gas in a tank. The gas may first pass through a catalyst tower that removes sulfur and other harmful ingredients from the gas before sending it to a condenser that converts it to liquid oil. The gas that is not liquefied is often led back into the reactor to act as fuel, and this greatly reduces the cost of operations. More cost information can be found: https://mswrecyclingplant.com/pyrolysis-plant-cost/.
Once the reactor cools it is possible to discharge the carbon black into which the waste has been converted, automatically. Carbon black is a byproduct of the pyrolysis plant that has several industrial uses. It can also be converted into carbon brick. Some plant operators who do not recover the steel before the feeding process may also collect the steel while the carbon black is collected. The gas oil can further be defined by waste oil distillation plant to produce diesel and other petroleum products, or even be used directly as a fuel in certain heavy industries.
Continuous pyrolysis plants have a low investment cost, where materials need to be smaller than 20 mm. These plants are auto feeding and will also discharge the carbon black automatically. Most equipment is modular with the majority of its components assembled at factories. They are equipped with a fully enclosed system that has special sealing systems that guarantee the complete safety of operation.